A fledgling startup founded by one of OpenAI’s first engineers is trying to “redefine manufacturing,” with factories powered by artificial intelligence to create precision parts to order.
Daedalus, as the company is called, is based in the southwestern German city of Karlsruhe, where its solo factory is currently housed. Here, Daedalus takes orders from industries such as medical devices, aerospace, defense and semiconductors, each requiring unique components for their products. For example, a pharmaceutical company may require a custom metal housing for a valve used in the production of a particular drug.
As it looks to ramp up operations with the goal of opening additional plants in its home market, Daedalus announced today that it has raised $21 million in a Series A funding round led by NGP Capital funded by Nokiawith participation from existing investors Khosla Ventures and Addition.
This brings Daedalus’ total funding past the $40 million mark, with other notable investors including Y Combinator (YC), which joined after Daedalus participated in YC’s Winter 2020 program.
The Daedalus factory floor. Image credits: Daedalus
Fragmented construction
The manufacturing industry — particularly in the manufacture of precision parts — it is extremely fragmented with almost every estimate. While it’s tempting to imagine that a typical manufacturing facility in 2024 is something akin to that of a large automotive assembly plant, that’s only true when high-volume products (like cars) are involved — the reality is somewhat different when you get down to the component level precision tools used in industrial machinery.
A company that has been designing industry-specific valves for decades probably won’t manufacture everything in-house. It will usually be based on an old fabricator network, which may mean working with a small business consisting of a single experienced “craftsman” and a handful of assistants working from a small facility.
“That means they’re not doing much in terms of digitization and it’s hard to change that because they’re used to working with pen and paper, basically,” Daedalus founder and CEO Jonas Schneider he told TechCrunch. “So you have these very low-tech manufacturers supplying the most critical components for these extremely high-end products.”
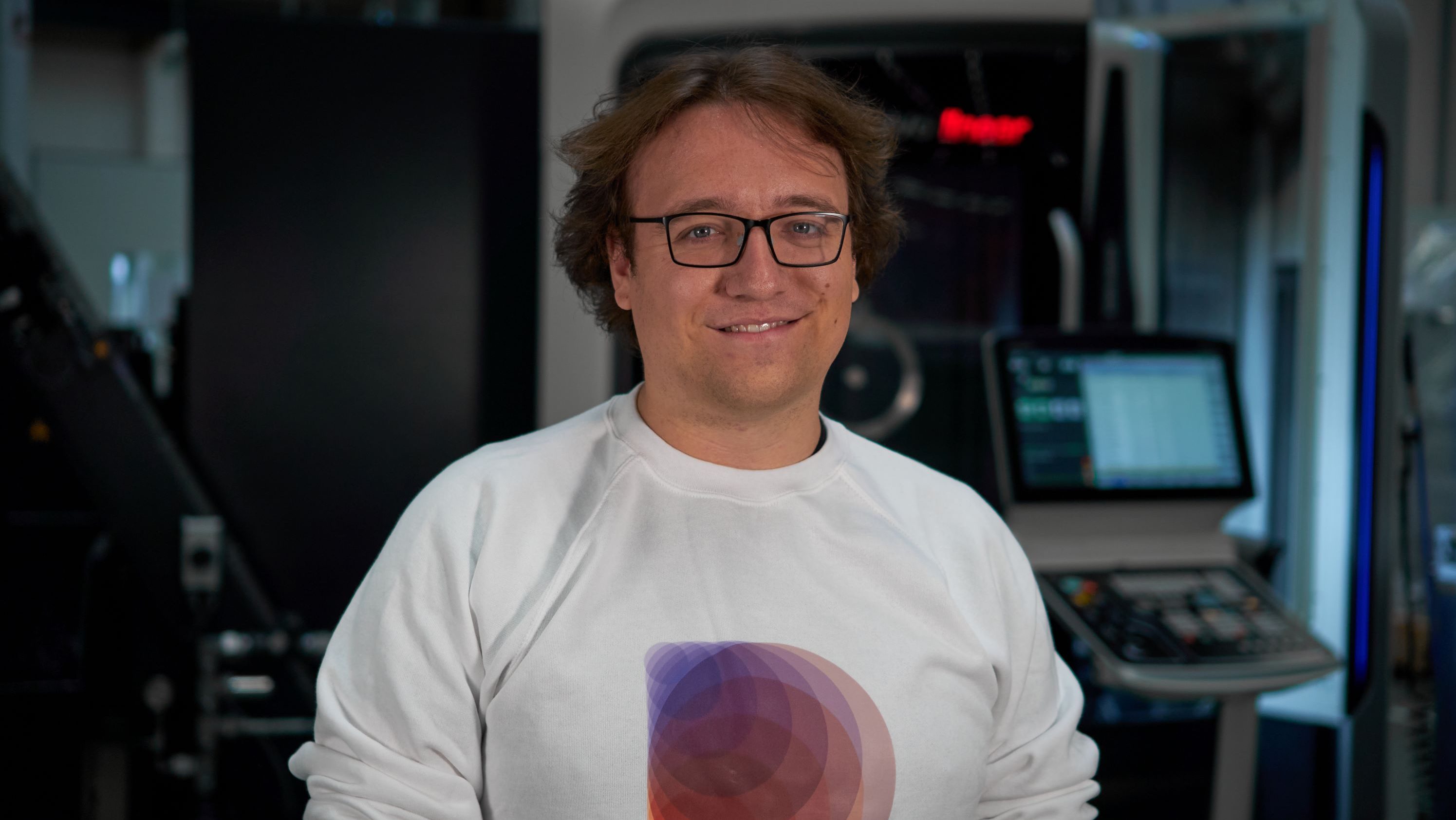
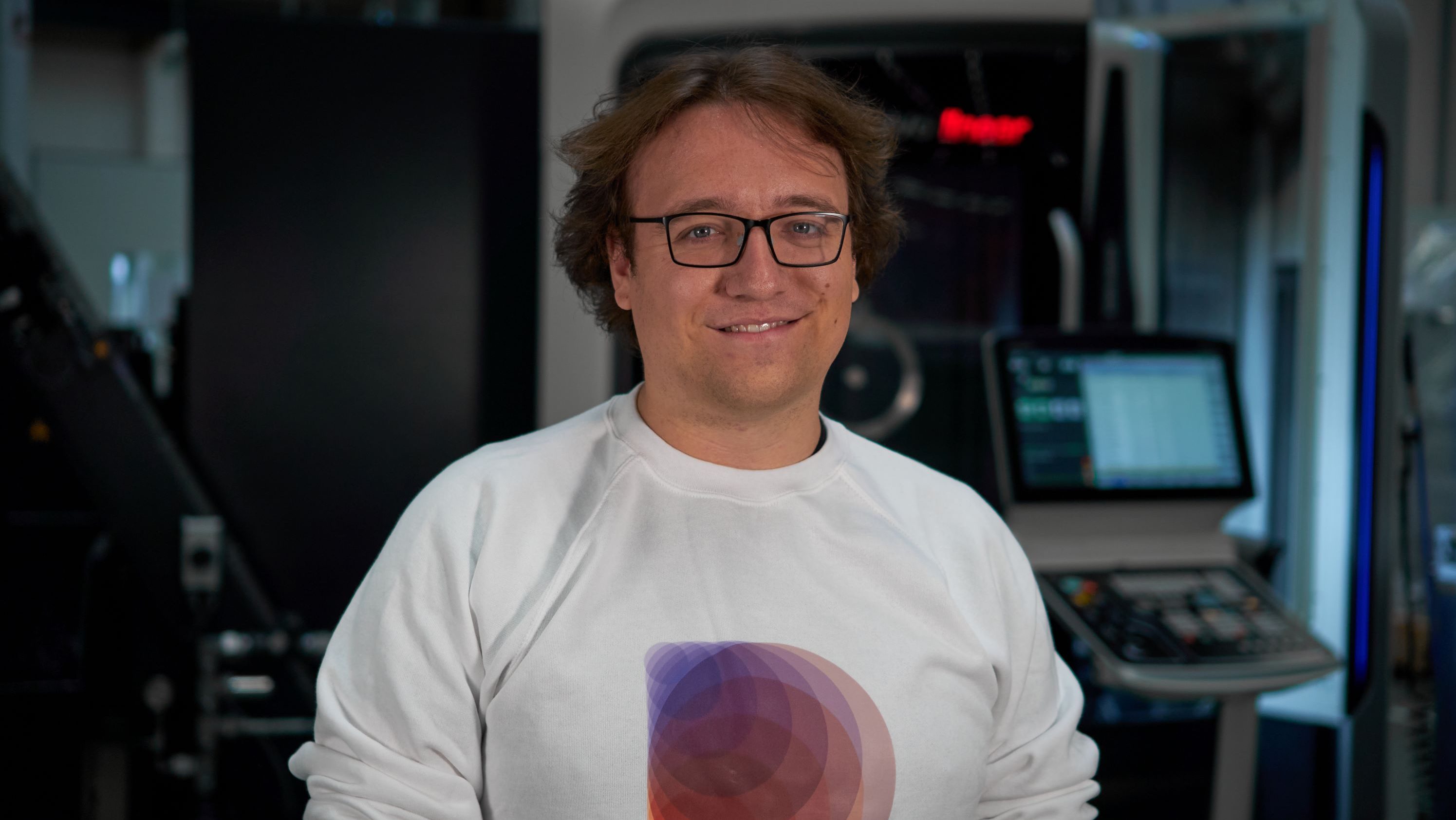
Daedalus founder and CEO Jonas Schneider. Image credits: Daedalus
Founded in 2019, Daedalus uses similar hardware available to any manufacturer, but its special sauce is in the software it develops on top to control and optimize the “shop” — that is, it automates many of the manual tasks involved in producing a specific component. So a customer will send in their CAD (computer-aided design) drawings as usual, and Daedalus develops those drawings into a finished part with automation running through the process.
“It’s about orchestrating all the workflows during production, planning and scheduling what’s running on the factory floor doing the work,” Schneider said.
For context, when production begins for a new “part” on a machine, there are typically dozens of steps and hundreds of decisions that affect what tools will be needed, what settings will be used to create the exact shape and dimensions of the part. and so on. And this is where Daedalus enters the fray – its software captures the data of manufacturing decisions of a “part” and uses it to guide decisions about how to create a similar part in the future. So a slightly larger valve, or a valve with an added component, may be essentially the same as a previous component, so Daedalus uses pattern matching to apply that previous knowledge to configure its machines for the new component.
In many ways, Daedalus expands on the core concept of 3D printing, which has been democratizing the manufacturing process for more than a decade. But with intelligent machine learning under the hood, it takes things to the next level—it’s like 3D printing on steroids.
“The comparison is very apt – as an outsider to this industry at first, it seemed to me that custom manufacturing had [already] solved with 3D printing. But mostly it’s due to technical limitations of the process,” Schneider said. “With 3D printing, it still means you have to design a new part specifically so that it can be 3D printed, and that actually ends up being quite an expensive process. But for the vast majority of the industrial base, it’s not really feasible and they can’t 3D print because it’s not accurate enough or the materials aren’t strong enough. You can frame what we’re doing, in a sense, as taking this idea from 3D printing and applying it to industrial-grade, high-quality components.”
The story so far
Prior to Daedalus, Schneider was CTO at OpenAI, where he was instrumental in launching the company’s robotics division in 2016. Indeed, OpenAI may be best known today for its flagship ChatGPT AI chatbot, but the company also ran a of robotics who conducted research on things like solving a Rubik’s cube with a robotic arma project that Schneider was directly involved in.
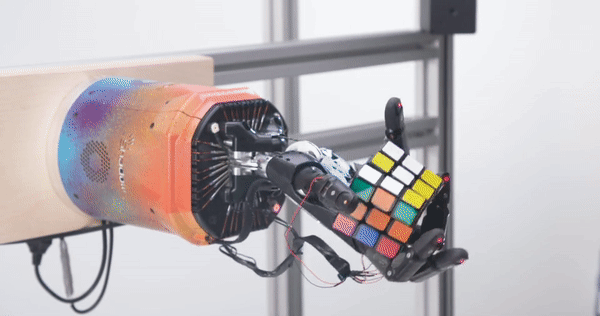
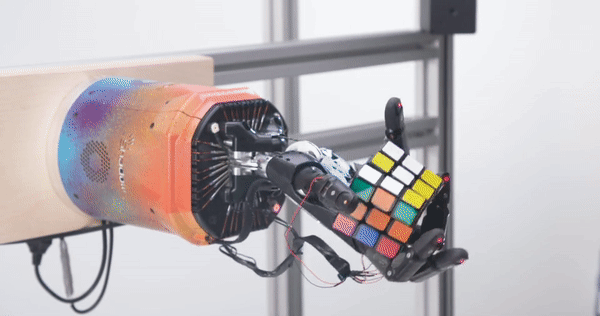
OpenAI’s Rubik’s Cube hand. Image credits: OpenAI
OpenAI after all broke up this group in 2021, but Schneider had led the operations side of software engineering for more than three years before leaving to start Daedalus in 2019.
While there were several reasons Schneider ended up leaving to create his own startup, it was an experience he encountered making a Rubik’s cube hand that played a big role in his decision to start Daedalus.
“At some point, the robot arm broke and we had to get parts,” Snyder said. “And guess what? They needed to be precision built. So there were these machines like ours today, but we had to wait months to get these parts. And I thought, why is it so hard to get parts here? All of that contributed to me to look a little more at this whole production space.”
Currently, Daedalus has a single 50,000 square foot factory in Karlsruhe from where it largely targets German-speaking markets, including Austria and Switzerland. In the short term, the plan is to expand to a second factory in Germany, and then further afield if demand is sufficient.
“This is the blueprint factory, right? This is where we learn all the systems and all the knowledge and distill it into how we make these parts,” Schneider said. “And then, in the long term, we’ll put those factories where our customers need them.”