Today, even niche industries have occupied souls looking for more environmentally friendly options for materials and processes, from laundry waste to artificial wool. Linggrove takes laminates — thin layers of wood and other materials — with a carbon-negative option that they claim performs better while looking just as good.
Laminates or veneers are common in every home and car: they’re the thin decorative wood or what have you that sits over the molded or printed body of a dashboard, appliance or even home trim. It is ubiquitous and, unfortunately, not always sourced or manufactured sustainably.
Lingrove has developed an alternative wood veneer made from flax fiber and plant resins that is carbon negative but results in a material they say is “very high stiffness, durable and resistant”, i.e. to touch, temperature and other materials (such as coffee ). They’re calling it “ekoa” — yes, in lowercase — and they’re hoping to break into cars and other interior surfaces with a new $10 million round of funding.
The Series B round was led by Lewis & Clark Agrifood and Diamond Edge Ventures, with participation from Bunge Ventures and SOSV.
The company claims that not only is its material better for the environment and just as good or better in terms of durability and so on, but that it can positively impact indoor air quality. Recycled plastic and other reused materials are a popular use for things like cabinets and trim, but they often lack the appearance, hardness, or other properties desired for such surfaces, and in some cases can release significant amounts of gas (this is your ‘new car smell’).
Image Credits: Linggrove
“We have a healthy air, low carbon, high performance and beautiful product,” said CEO Joe Luttwak. “The use of post-industrial raw material can, in some cases, be positive for the environment. However, many of these by-products still emit VOCs [volatile organic compounds] which are detrimental to indoor air quality and cannot be converted into high performance materials.”
ekoa materials perform well, don’t leak weird gases into your kitchen or car cabin, and look a lot like regular wood. It can be modified to have various shades or opacity and generally has all the advantages of man-made laminates while being carbon negative and can be ground and reused when retired.
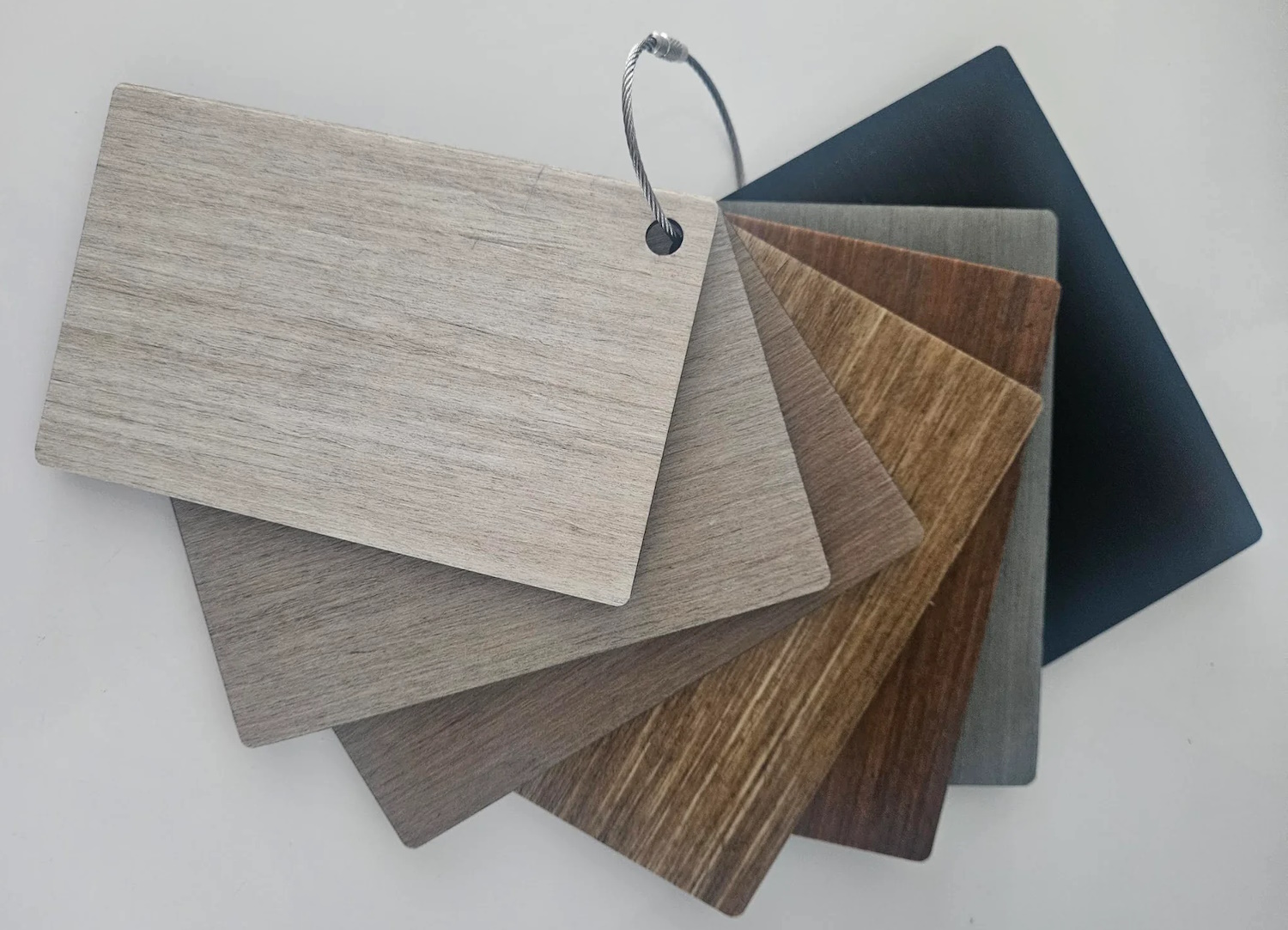
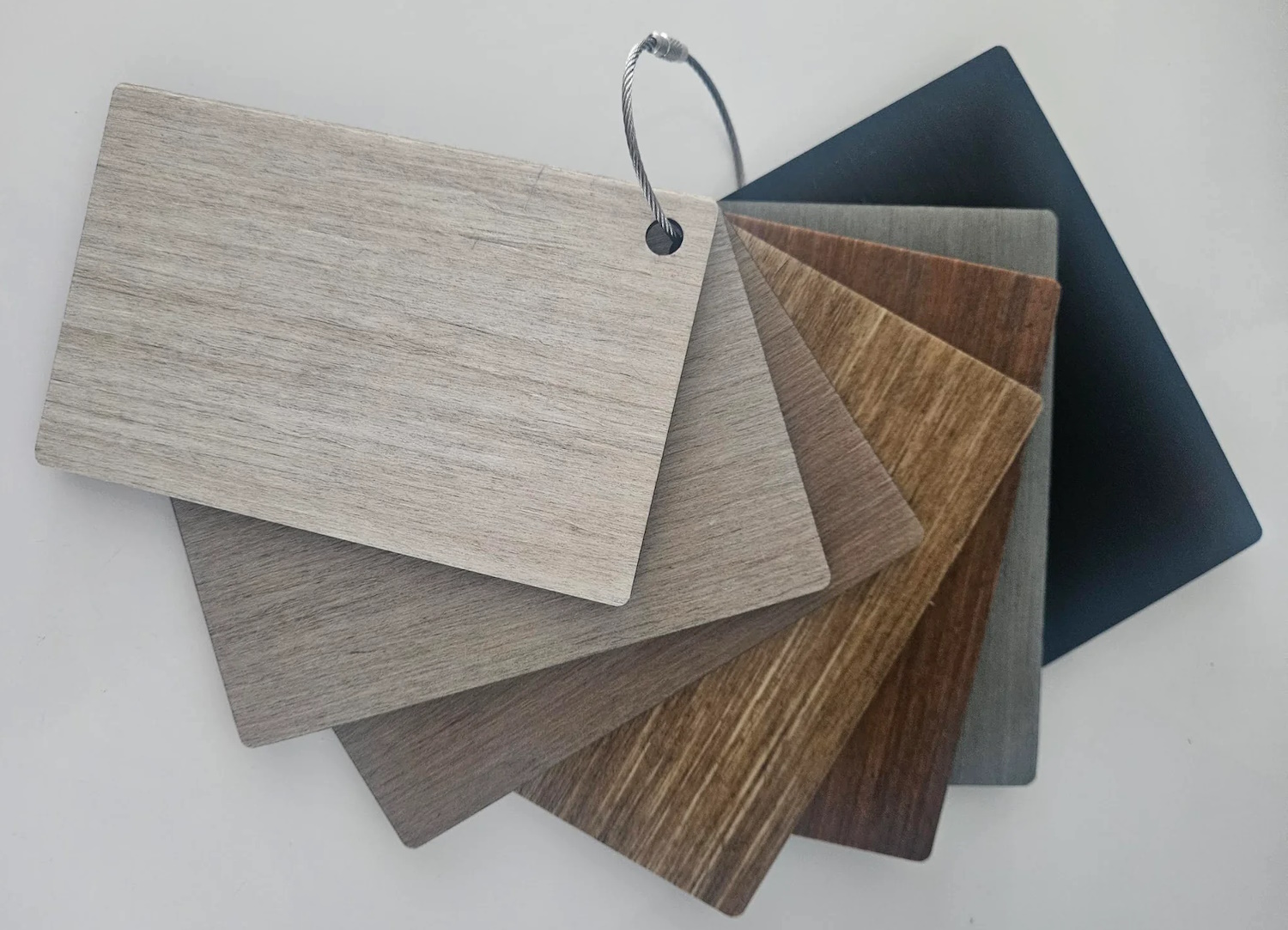
Image Credits: Linggrove
You might wonder, as I did, why not use real wood — things like sawdust and wood chips that already come from industrial wood-handling processes? These, Luttwak said, are perfect building materials — that is, whatever is in the middle of a board — but they are not decorative. There’s a reason why MDF boards and the like tend to have at least one side covered in veneer: the interior wood-glue mixture isn’t attractive or particularly resistant to things like solvents and oils.
Veneers aren’t exactly the most high-profile or exciting business to take on, but it’s always encouraging to see innovation taking place in corners of industries where a smart alternative can scale millions of products and make them at least a little less wasteful.
The new investment will help the startup from small-scale in-house production to fulfilling all pre-orders and expanding into the automotive world.